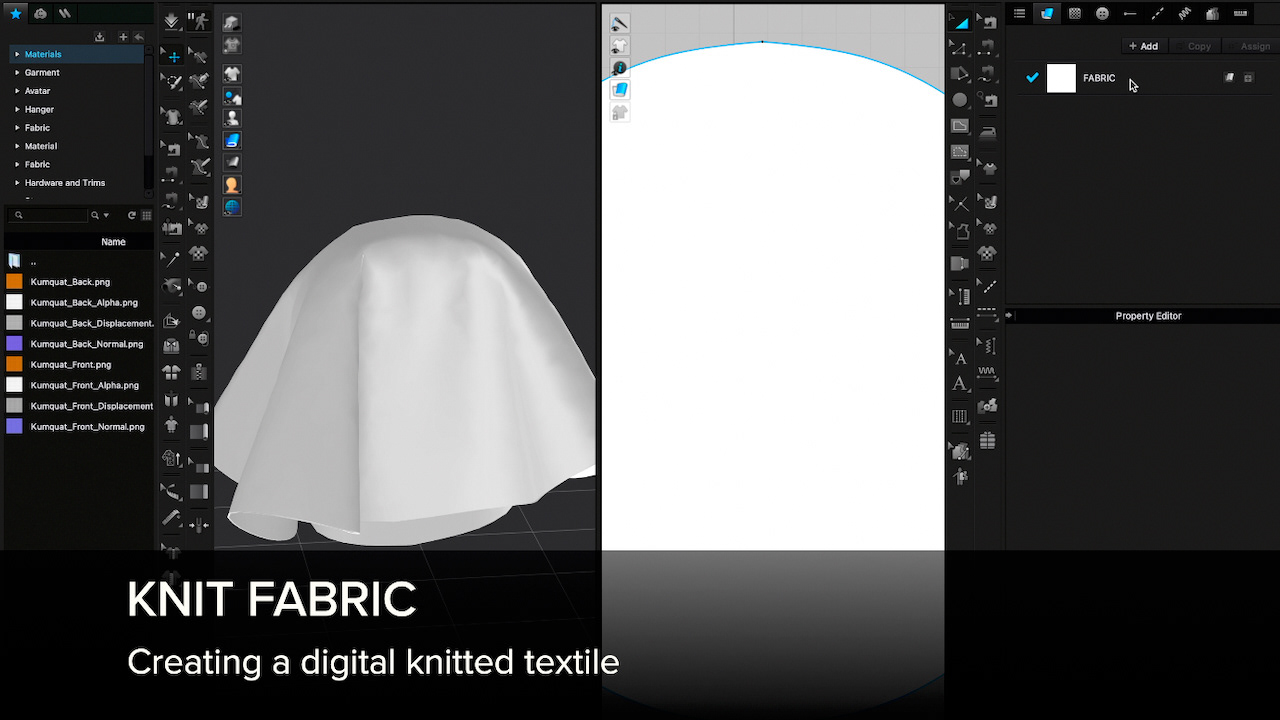
Digital textiles are a subcategory of digital materials. They can be significantly different to one another, such as plastic, steel or wood. Currently, in most 3D software, they are all created in the same way, regardless of their construction, woven, knitted, or non-woven. In practice, the process is as follows: Image layers are assigned to a blank ‘default fabric’ and the physical properties are described by filling out the list of pre-determined physical property parameters. Both these primary inputs are used by the render engine to simulate the material, described as physical based rendering (PBR).
In this tutorial on YouTube I illustrate the textile creation process in 3D garment software CLO3D.
This process is accessible, easy to learn and therefore fit to be integrated into the fashion design and development workflow. The time it takes is determined by the desired simulation accuracy, ranging from 15 minutes to multiple hours, by which 15 minutes cover when images are available and the ‘physical parameters’ preset is used. It can take half a day’s work if physical measures are taken manually using a fabric emulator in combination with fabric scans. The timing for the latter really depends on your usage frequency and workplace set-up.
As the creation of texture maps from scratch is time consuming and requires knowledge of repeat pattern tiling, companies like TG3D provide tools such as textile scanners and scanning apps for speeding up and facilitating the creation of digital fabrics. Similarly, the measurement of physical fabric properties for simulation purposes is facilitated by using fabric emulators, such as CLO3D’s or Browzwear’s models. However, it is much quicker to use existing content, therefore sourcing digital fabrics is a viable alternative.
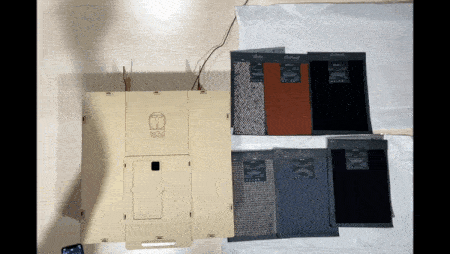
Scanatic™ Nuno Fabric Scanner (Image: Scanatic, 2023)
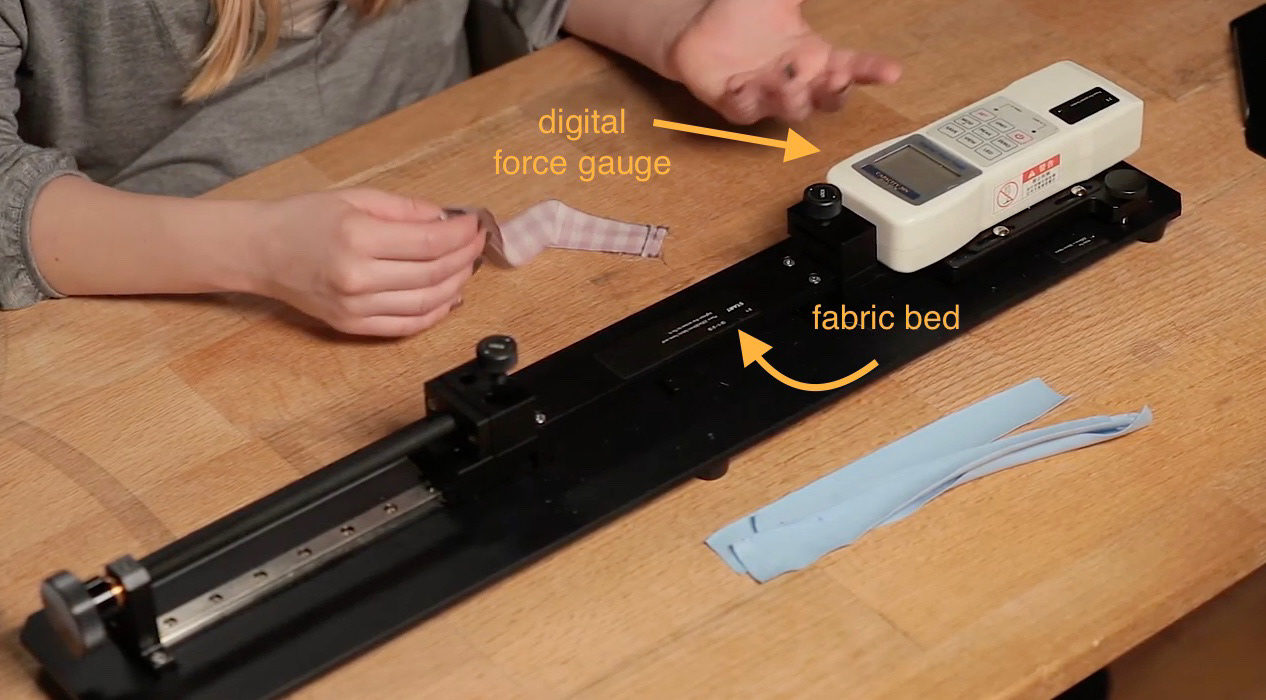
CLO3D fabric emulater (Image: CLO3D, 2022)