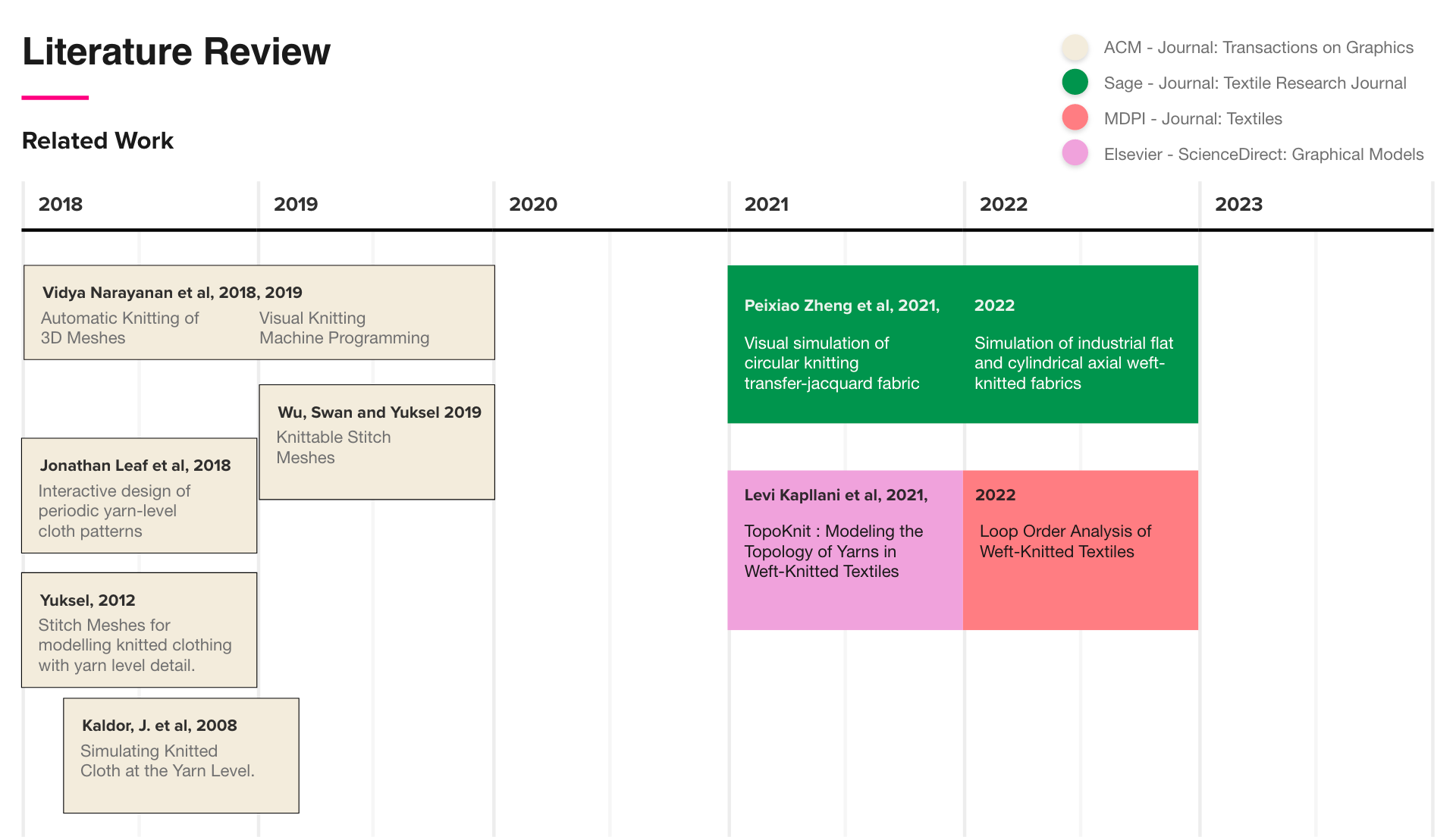
Referenced Research Articles, Colour coded by publisher (Infographic Literature Review, 2022)
Computerisation and automation are the important drivers of technological advances in garment production. Digitisation of textile machinery paves the way for software advances and ultimately for more automated production processes (BoF and McKinsey, 2022). Research in knitted textiles advanced due to the growing demand of data and simulation needed by various industry sectors (Kapllani, 2021; Yuksel, 2012; Narayanan, 2019). This demand engaged a multi-disciplinary group of researchers, active in the field of material science and computer science, accelerating the progress in the last two decades. Most articles concerned with knitwear simulation are published by ACM, Sage Journals, MDPI and Elsevier.
Publishers and Journals
ACM, the Association of Computational Machinery has a reputation of being the destination for computer scientists, knit simulation being a new addition to its Transactions on Graphics (ToG) which is a learned and foremost peer-reviewed journal that provides the forum SIGGRAPH on which computer graphics related subjects are discussed. Similarly, knitwear simulation papers appear in peer-reviewed The Textile Research Journal by Sage Journals, dedicated to combining knowledge in materials, chemistry, manufacture and system sciences related to textiles and fibres. Pioneering in scholarly open-access publishing since 1996 is MDPI, a swiss publisher. Their journal Textiles and its special issue New Research Trends for Textiles were launched recently in 2020. Lastly, Elsevier is notable for its peer-reviewed platform ScienceDirect, with Graphical Models, one of their 2700 journals, in which Kapllani’s foundational, process-orientated article was published.
The applications of knitted textiles are not just increasing in consumer products, namely fashion, furniture, and automobiles, but also in other industries such as architecture, composites, medical, and military (Kapllani, 2021). As a consequence, research into knitted textiles in computational and material science has made significant advances in recent years, from which the fashion industry can benefit and learn. My work focuses on the advances concerned with knit simulation and data compatibility with computer programmable knitting machines.
Findings in Computational and Material Science
The foundational, ground-breaking work for today’s knit simulation has been done by Jonathan M. Kaldor and his team at Cornell University, Ithaca, NY; the research conducted has been widely referenced in subsequent, related work. The team developed a yarn-level physical model for knitted textile simulation, proving it based on a range of knit stitches such as garter, stockinette and rib (Kaldor et al., 2008; 2012). This was possible due to Gröller’s (1995) research, the modelling of knitwear by using repetitive volume data sets.
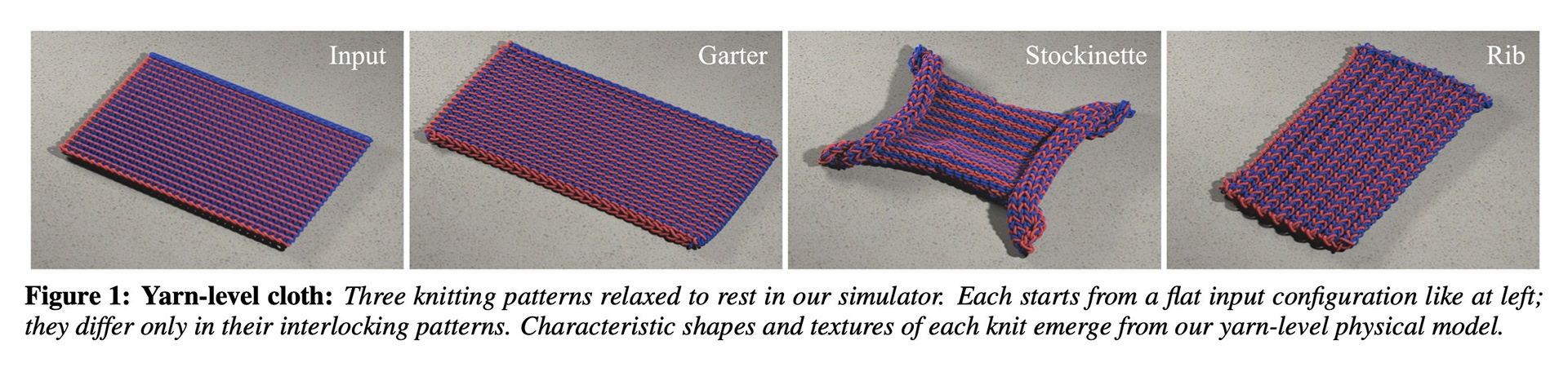
Simulation of Knitted Cloth at Yarn-Level (Kaldor et al., 2008)
However, Leaf (2018) notes that, at the time, yarn level simulations were notoriously slow, and therefore it was unfeasible to think of interactive performance. Four years following Kaldor’s advances, Yuksel et al. (2012) successfully proposed stitch meshes to improve knit simulation in speed through a novel approach to representing knit stitches on 3D meshes.
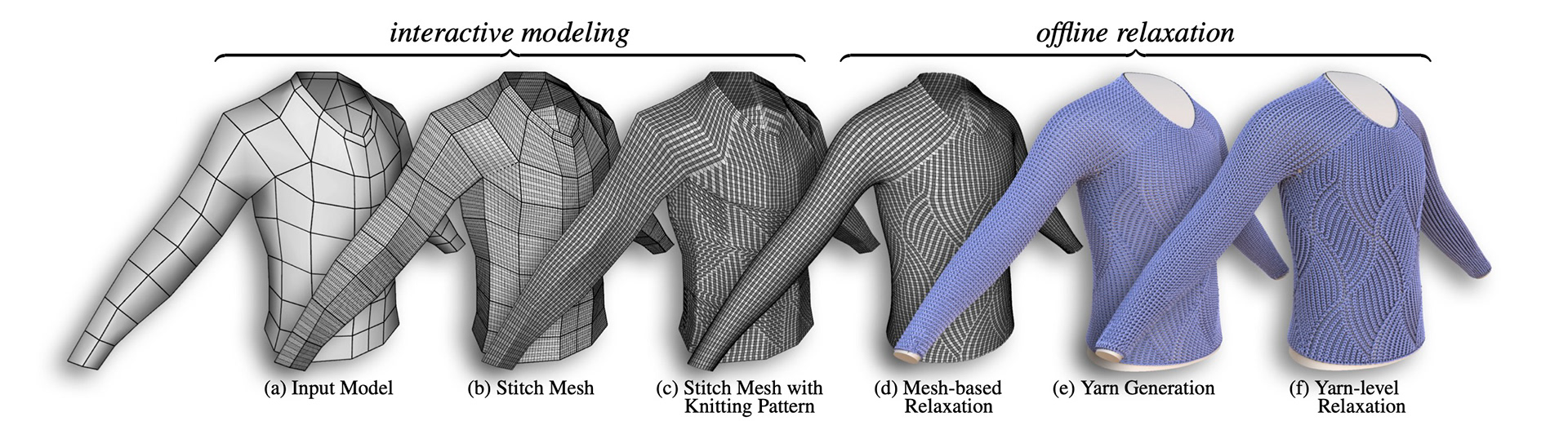
Stitch Meshes (Yuksel et al., 2012)
At the University of Utah, Yuksel continued his work and supported the work of fellow researchers, notably Wu and Swan. Over the coming decade, their work, Knittable Stitch Meshes proposes a fully automated method for converting arbitrary 3D shapes into knit stitches, its success shown based on the - in computer science - famous Utah teapot, simulated and industrial machine-knitted (Wu et al., 2019).
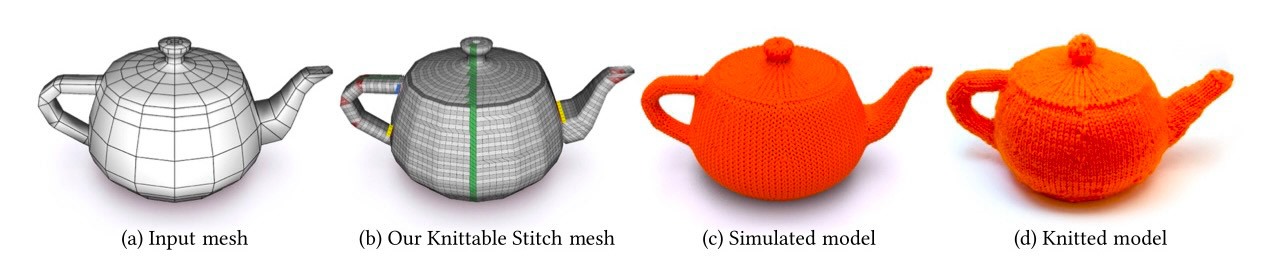
Knittable Stitch Meshes (Wu et al., 2019)
Around the same time, the trio’s research was mirrored by another group of researchers operating from Carnegie Mellan University, led by Vidya Narayanan, contributing to the efforts to make simulation knittable. Narayanan (2018) and her fellow researchers developed an original approach automating the knitting of 3D meshes. The first knitwear simulations by specialised industrial knit software, such as APEXFiz released in 2021, were probably built upon this work.
Finally, members of both Universities collaborated on Visual Knitting Machine Programming, introducing yarn geometry and finally being able to convert any stitch mesh into a knittable structure for computer-controlled knitting machines (Narayanan et al., 2019).
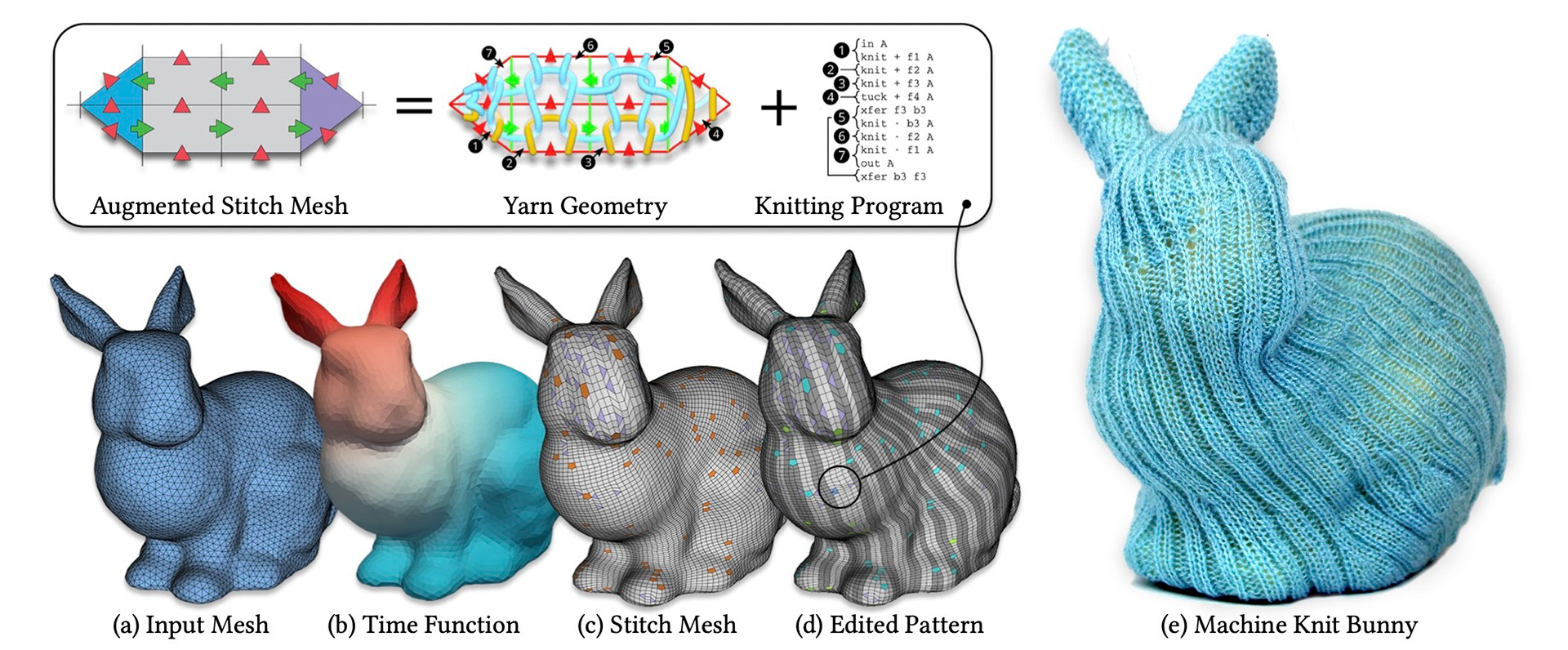
Visual Knitting Machine Programming (Narayanan et al., 2019)
Since its introduction, this method has been built upon and its simulation speed significantly increased whilst the calculation amount is reduced using the physical-geometric hybrid method. (Sha, S. et al., 2021).
Circular knitted transfer-jacquard fabrics, as designed and manufactured at BYBORRE for instance, have been optimised through Zheng et al.’ s work, consolidating information retrieved from a transfer-jacquard design program and simulation using an illumination model and coordinate mapping to achieve an optimised representation (Zheng et al., 2021). The outcome surpasses the current representation of Create by BYBORRE, providing the industry with the opportunity to implement this research in the area of circular weft knitted jacquard representation, potentially applicable to warp-knitted fabrics.
Significant contributions to pave the way for universal knittable machine output were initiated by Kapllani et al. 's (2021, 2022) research. It defines a foundational data structure for representing the topology of weft-knitted textiles at yarn level with the goal to represent all knitted fabrics that can be manufactured from a specific set of stitches and is guaranteed to represent only physically valid states of the fabric.
Kapllani’s et. al’s proposal, prompted a number of questions; Could the foundational data structure, integrated into design software, lead to further automation that streamlines the creation-to-production process, namely saving control and trouble-shooting time? For instance, could it provide reliable, automated tension settings and viability of knit structures taking various yarn properties into account? Similarly, would a universal data output lead to the potential use of any kind of knitting machine? Or any flat knitting machine, but independent of the machine manufacturer? And this in turn could facilitate the maximisation of the use of available knitting machines?
Having examined the innovation potential of knit simulation software, the next section will look at
‘Environmental Opportunities’.
‘Environmental Opportunities’.